Rebelのウィンカーステー部品を3Dプリント(1)
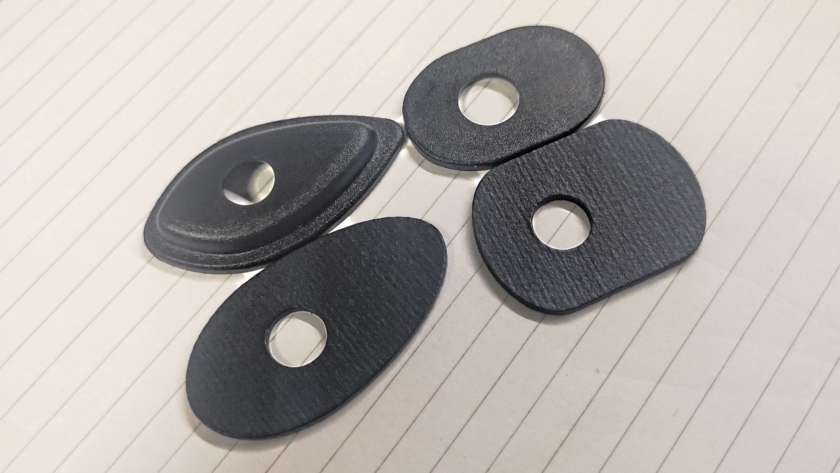
Rebel のウィンカーステーを3Dプリントサービスを使って自作してみたのでその記録を紹介します。 取り付け記録については別途また記録します。
この話は Rebelのウィンカーステー部品を3Dプリント(2) に続きます。 (2) では、実際にプリントした部品の販売ページも案内しています。
作る切っ掛けと問題
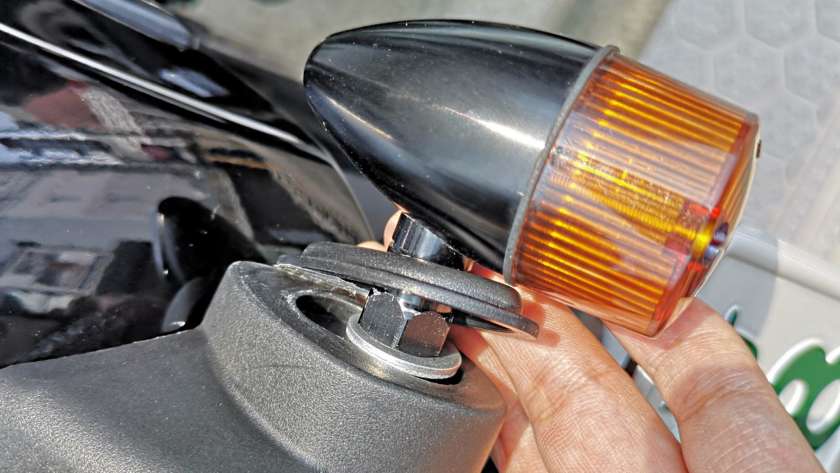
以前までは Kijima から販売されている公式の製品を利用していました。Rebel のカスタマイズ例でも紹介されている程度にはメジャーなのですが、 少々欠点があって、ステーの間に空間があり、取り付け車種やウィンカーによっては硬く固定できません。さらにステー自体は樹脂製ですから強度が甘く、 あまり強く回すと破損してしまいます。
これについては「Rebel ウインカー交換(4)-リア・テールランプ編」の記事を参考にしてください。
そしてこれが問題を引き起こしてしまって、1年点検でバイクを預けたところ 「ウィンカーが手で回転するのを直している都合で、仕上がりまでに時間がかかります」という旨で電話がかかってきました。 走行には問題ない程度の取り付け強度ですので、これについては「整備屋さんたちからすると、きちんとしないといけないのかな」と思ったのと「すでに作業に入っている」というのとで、 その場では了解したのです。このとき「取り付け作業しますか?」の連絡であれば、事態は変わっていたことでしょう。
そして帰ってきたのが、写真の通りの無残な取り付けです。正直プロの仕事とは思えないし、結局は手で回転してしまうし、元のパーツは雑に穴が加工されています。 黒塗りの部品にはあて布などせずに傷が入りまくってますし、これはどうしたものかと思いました。なんであれば、作業前より危険な状態です。 ちょっとの振動でずれてしまってウィンカーが外れる。
この件については本当は怒ろうと思ったんですが、その場では確認できなかったことと、一応の電話が入ってそれを了解してしまったこと、 何よりほかの整備についてはきちんと対応してくれてるし、悪意がなかったと信じたいのです。
とはいえ「二度と任せるまい」という気持ちで、じゃあ完璧に取り付けてやろうじゃないかとオンリーワンの部品を作ることにしました。
技量と知識量の差は大きい気がする
余談ながら、バイク周りの整備点検をしてくださる方、商品販売する方たちの技量や知識量の程度の差には結構驚かされます。 振り返ってみて取り付け施工が恐ろしく雑で説明が一切ないピットや(おそらく初心者で足元見られたであろう)、 公式の仕組みに従ってサイズ選びをしない「公式ライセンス持ちの」ヘルメットの販売店員さん、 そして今回のちょっと残念な整備士さん。乗り始めて1年足らずで既に 3 人に泣かされています。
これに関しては私が初心者ということもあり、それこそ勉強不足でお任せするだけの形になったのが問題ありとも思いますが、 それにしても初心者に対してやることじゃないよな、と残念な気持ちにさせられています。
なんせ素人の自分がきちんと調べたら公式で情報が提供されていたり、少し練習した程度でマシに施工できるのだもの。 少なくともこういう方法はどうですか、とか提案することができる。
私のスタンスとしては、知識や技術に敬意を以て料金支払うことには躊躇がないのですが、困ったものだなと思いました。 業界がにぎわってないとそうなるんですかね。
一方でバイク専門の塗装業者グローバルの担当様、 マフラーパーツの輸送時破損の際には真摯的かつ迅速に手配を進めてくださった BEAMS 社および代理販売店の担当の方、 ヘルメットについて丁寧に説明してくださった 2 りんかん一之江の販売担当の方、 ならびに硬くなったナットを専用工具で快く外してくださったピットの方には感謝するばかりです。
部品製作に利用したサービス
3D (CAD) モデリング
パーツのモデリングには Autodesk 社の TINKERCAD を使いました。Autodesk 社は業界最大の 3D CAD データを制作するツールを開発・販売しています。 ところがこの TINKERCAD は大層簡単なツールで、(1) Web ブラウザのみで設計とファイル出力が可能で (2) 基本的な操作は、拡大・縮小・回転・基本形を足す、基本形を引く、だけで完結します。
恐らくですが、無料で使えて、Web ブラウザだけで完了し、操作が最も簡単な、実寸ベースのモデリングツールです。 代わりに複雑な形状を作ったりすることはできませんが、今回の部品を作るくらいは簡単にできました。
プリントサービス
プリントサービスには DMM プリント を使いました。国内では比較的安く、いろんな素材を選択できることからです。 あと必要なら部品の販売もできるという点も魅力的です。
まぁ比較的安くとはいえ、それなりに値段がかかります。Kijima のパーツが 1 セット 700 円程度なのに対し、DMM プリントで作った自作のパーツは 1 セットで 3,300 円ほどになりました。 金型を使った量産品との差異ですね。
部品は「MJF」で、以来から 8 日ほどで手元に届きました。思ったより早い!必要なら家庭用 3D プリンタ以外の素材でも作れるのが魅力的です。 家庭用で試して、別の素材でっていうのが理想的ではあるのですが、家庭用を購入するほど力を使わなくても、今のところは良いかなという考え方でした。
今回選んだ MJF は表面が多少荒いものの、そこそこ耐久性があり、安く、早く、黒があるという素材です。
出来上がった部品の説明
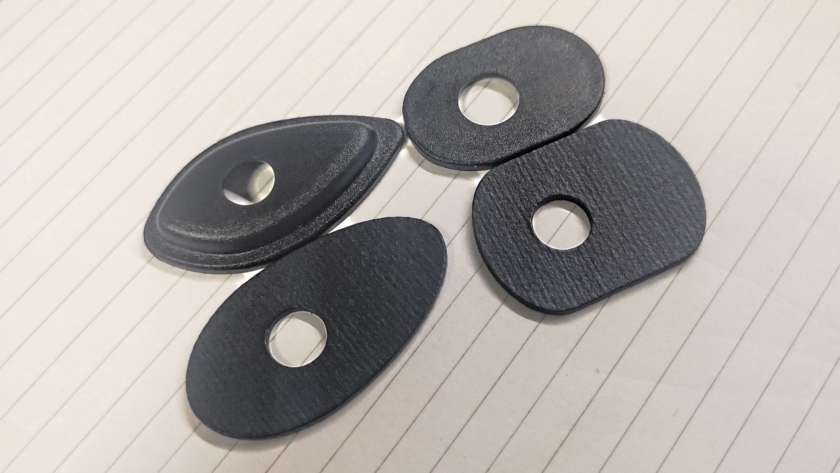
Kijima の純正品とは少々形が異なりますが、問題を起こしていた裏面の空間がなく、純粋なプレート上のステーができました。
縞模様ができてしまってますが、これは「積層方向」を指定しなかったためです。要するに印刷する方向ですね。 モデルデータは薄い方を上にして提出しているのですが、実際に印刷されたのは長辺の方向でした。
これについては指定できることを知らなかった私が悪いと思うのですが、それにしても納品したデータと反対方向に印刷されるのは想定外で、 時間かかっても良いので連絡欲しかったところですね。少し残念。まぁいい勉強です。 皆さんがもし挑戦するときは、積層方向に注意するようにしてください。
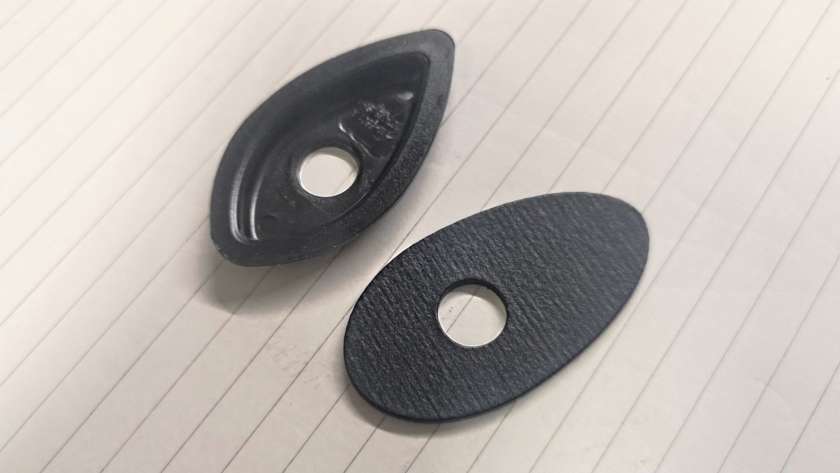
もう 1 つ、裏面のステーも幅を大きくして設計しています。写真の上の列が Kijima 純正品、下の列が今回制作したものです。 ウィンカー両側ですから、合わせて 6,600 円くらい、高い買い物ですね;
強度については積層方向のためか、当然のように縞に沿って折り曲げると純正品より弱い感じです。 クランプした時の強度については取り付けたときに分かるかと思います。 何せリアウィンカーは結構気合い入れて取り付けないといけないですから、なかなか手を出せず…。 本当に整備士の方はいらんことをしてくれました、悪意ないだろうとはいえ…。
この話は Rebelのウィンカーステー部品を3Dプリント(2) に続きます。